8 Key Steps Before Selecting an ERP System for Manufacturing
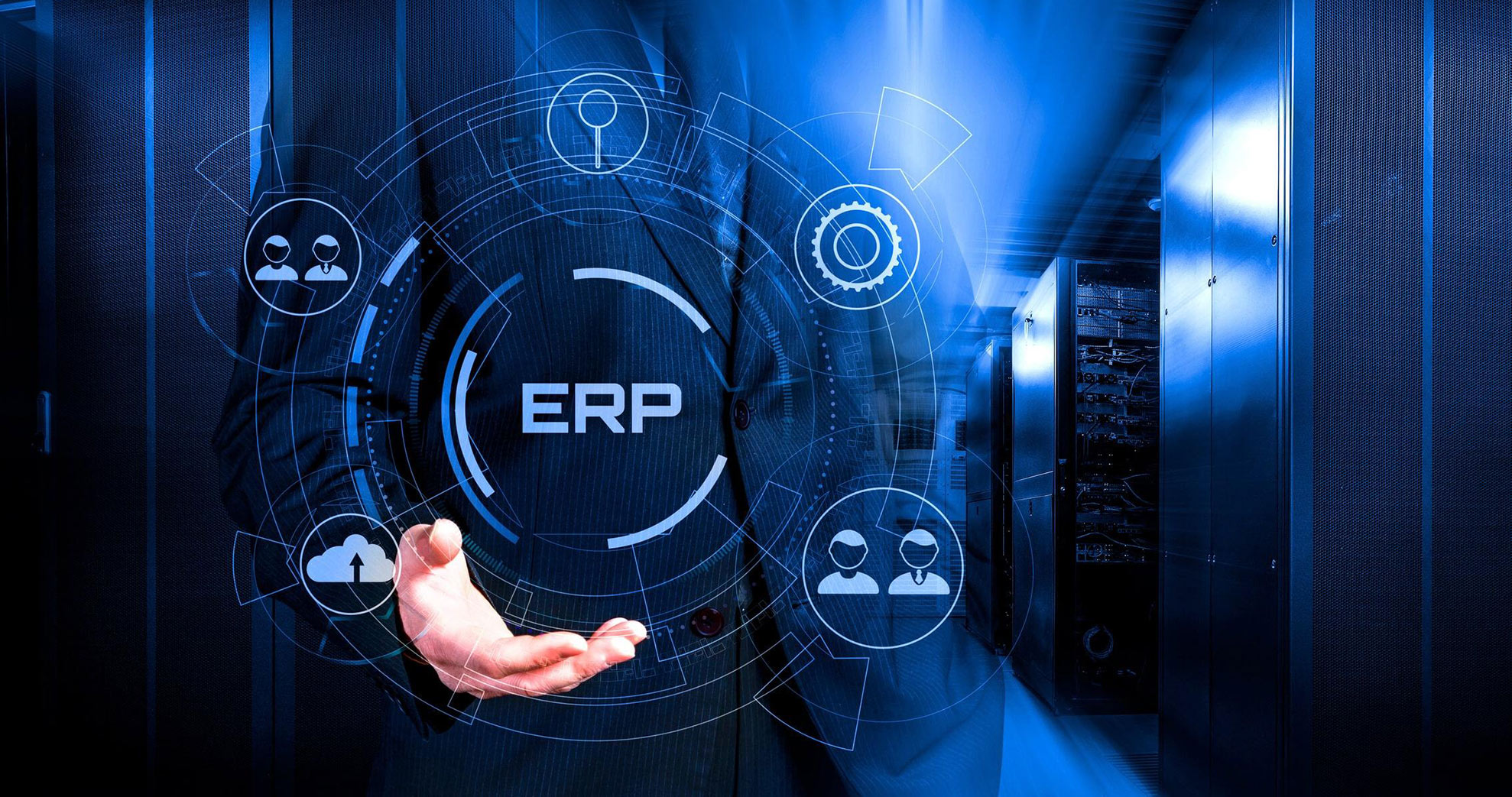
- August 22, 2023
- Jhansi Rani
- 0
Assess Your Requirements and Goals
Explore your manufacturing processes, business objectives, and the specific ERP functionalities supporting your operations. Begin by thoroughly analyzing your current workflows, identifying pain points, bottlenecks, and areas for improvement. Define your manufacturing processes from raw material acquisition to finished product delivery while outlining your business goals. These goals can guide your ERP selection process and ensure alignment between your system and strategic direction. Identify the features your manufacturing environment requires, such as inventory management, production scheduling, quality control, and supply chain visibility, to understand your unique needs and inform subsequent decisions.
Engage Key Stakeholders
Define Your Requirements
Once you’ve gathered insights from stakeholders, compile and prioritize a detailed list of requirements for your ERP system. Consider features such as inventory tracking, demand forecasting, real-time reporting, compliance with industry regulations, and the ability to support various manufacturing methods and assign priority to each aspect. Prioritization guides your decision-making process later and ensures that essential functionalities are not compromised, even if trade-offs are required. The more precise and comprehensive your requirements list, the better you’ll be able to evaluate potential ERP solutions.
Research and Shortlist Vendors
Once you understand your manufacturing requirements and goals, undertake comprehensive research to identify ERP vendors specializing in manufacturing solutions. Look for vendors with a long, proven track record in your industry and evaluate their reputation for delivering reliable and scalable systems. Compile a list of potential vendors and assess each vendor’s ability to accommodate your manufacturing complexities, such as production variations, supply chain intricacies, and quality control standards. Narrow your list to a handful of vendors whose offerings align with your needs and ensure their systems can handle your expected growth and future demands. A well-researched shortlist sets the stage for more in-depth evaluation and selection.
Conduct Evaluation and Demos
Engage with the shortlisted ERP vendors to gather detailed information about their systems and send them a Request for Information (RFI) or Request for Proposal (RFP) document outlining your requirements. Evaluate their responses based on their technical expertise and how well they understand your specific manufacturing challenges. Request live demos or proof-of-concept (POC) sessions where the vendors can showcase how their systems address your needs. Involve key stakeholders from different departments to participate in the demos and provide valuable insights, allowing you to make more informed decisions.
Perform Integration and Security Checks
Incorporating an ERP system into your manufacturing ecosystem requires seamless integration with existing tools and software. Assess the shortlisted vendors’ integration capabilities and compatibility with your current technology stack. Consider how well the ERP system can connect with your finance, inventory management, supply chain, and other critical applications. It will determine how efficiently data flows across your organization, reducing manual data entry and minimizing errors. Ensure the vendor follows the best data protection, storage, and access control practices. Also, verify that the ERP system complies with relevant regulations with features like user authentication, encryption, and audit trails.
Negotiate and Finalize Contracts
Implement and Train Your Workforce
After signing the contract, focus on the practical implementation with a detailed project plan outlining each phase, task, responsibility, and timeline. Allocate resources and ensure that you have a dedicated project manager who oversees the ERP system implementation process. Begin by setting up the infrastructure, configuring the ERP system, and conducting comprehensive testing to identify and rectify any issues before the system goes live. Ensure thorough training for your employees with tailored sessions that cover system navigation, data entry, reporting, and any specific workflows relevant to their roles. Hands-on training can help users become comfortable with the new system and maximize its benefits. Regularly communicate updates and progress to stakeholders to manage expectations and ensure a smooth transition. Closely monitors the system’s performance post-launch and addresses any teething problems promptly. Continuous improvement is critical to your implementation strategy, ensuring that the system evolves to better support your manufacturing operations over time.
Why Oracle ERP Cloud Services?
Oracle ERP Cloud solutions integrate manufacturing processes, from supply chain management and production planning to quality control and inventory tracking. This streamlines data flow across different departments, reducing data silos, redundancies, and manual entry errors. Additionally, Oracle ERP Cloud Services offer robust analytics and reporting capabilities, enabling manufacturing leaders to monitor KPIs, track production efficiency, and identify areas for improvement. With actionable insights readily available, manufacturers can optimize their production processes, reduce waste, and improve resource utilization. Predictive analytics allow manufacturers to anticipate demand fluctuations in advance and adjust production plans accordingly.
Why Rite Software?

Services
Products
Company
Copyright © 2025 Rite Software Solutions & Services LLC. All rights reserved.